|
|
|
HOME > ±â¼úÀÚ·á> °ü·Ã³í¹® |
 |
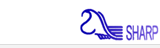 |
|
|
|
|
|
[JMPT (½ºÀ§½º/SCIE)] Precise glass microstructuring with laser induced backside wet etching using error-compensating scan pat¡¦ |
±Û¾´ÀÌ : °ü¸®ÀÚ
Á¶È¸ : 1535
|
|
Æ®·¢¹é ÁÖ¼Ò : http://sharp-eng.com/web/bbs/tb.php/group_02_b_03/199
|
https://www.sciencedirect.com/science/article/pii/S0924013621000066 (1016) |
|
ÇмúÁö¸í: Journal of Materials Processing Technology
¹ßÇà±¹°¡: ½ºÀ§½º
¹ßÇ¥ÀÏÀÚ: 2021³â 5¿ù
SCI¿©ºÎ : SCIE
¿ø¹®Link: https://www.sciencedirect.com/science/article/pii/S0924013621000066
Á¦¸ñ: Precise glass microstructuring with laser induced backside wet etching using error-compensating scan path
ÀúÀÚ: ±Ç±Í°¨(¼¿ï´ëÇб³) ¼Û±â¿µ(»þÇÁÁ¤¹Ð) ¼Àç¹Î(¼¿ï´ëÇб³) ÁÖÁ¾³²(¼¿ï´ëÇб³) ¾È¼ºÈÆ(¼¿ï´ëÇб³)
³»¿ë: ·¹ÀÌÀú¸¦ ÀÌ¿ëÇÏ¿© À¯¸®¿¡ ¹Ì¼¼ÇÑ Çü»óÀ» °¡°øÇÔ
ÃÊ·ÏAbstract: Laser induced backside wet etching (LIBWE), a simple-setup process capable of processing transparent materials, has been studied to overcome difficulties in glass micromachining. However, LIBWE still show practical difficulty in machining various glass applications due to the crack occurrence and unprecise final geometry. This study proposes the error-compensating scan path generation method for the precise fabrication of glass microstructures without additional devices. In conventional scan paths, the overlap of scan path¡¯s initial and final points, constant scan path patterns and uneven distributions of laser irradiation were the leading causes of geometric errors. The scan path generation method was developed to minimize or eliminate the causes of geometric errors in conventional scan path methods. Machined results, with error-compensating scan path, showed the removal of significant error from conventional paths with proper material removal rates. The effects of scan path generation parameters on the machining characteristics were also investigated. By adjusting the scan duty ratio and laser irradiation distribution of the entire scan path, micropockets with an average surface roughness of 0.26 ¥ìm could be processed at a material removal rate of 29,700 ¥ìm3/s. Based on machining characteristics of the errorcompensating scan path, various glass microstructures were fabricated and the feasibility of the proposed method was verified.
|
|
|
|
|
|